Smart Machinery, Smarter Leadership
Talent Strategies for the Digital Age
A recent report in The Economist called the digitization of manufacturing “the Third Industrial Revolution” and convincingly suggested that software advances, additive manufacturing, high tech materials and a host of other technology breakthroughs will radically change how practically everything gets made. In the Machinery sector, software advances have wrought only minor disruption thus far. Machinery has evolved, certainly, but few would say it has been transformed. Nonetheless, the technology to transform the sector exists, is largely proven, and is waiting to be applied. This paper encourages Machinery sector executives to look squarely at the potential for disruptive change and invites them to explore what they can do to make the wondrous possibilities of the Digital Age their own company’s competitive advantage.
Convergence
Some Machinery companies are already applying advanced technologies to excellent effect. For example, as Asian companies leverage cost and volume advantages to grab significant share of the global market for more standardized kinds of machiner y, firms in the West and Japan increasingly focus on crafting “smart” machines, automated solutions, and complex systems and services finely tuned to specific customer needs. Further, many Machinery manufacturers are heavily investing in optimizing their global supply chains via sophisticated systems integration. In terms of the products and solutions Machiner y companies offer, however, software capability has mainly been applied via embedded controls and in a non-networked structure.
The new frontier is convergence – the comprehensive blending of mechanical engineering with software engineering (as well as with electronic, computer, control and systems design engineering) from product and system concept through dev elopment, manufacturing, maintenance and service. Much is at stake. The merging of technologies and engineering disciplines to produce sophisticated new solutions will increasingly blur the lines between previously distinct industries. Effective early adopters and bold new entrants will rewrite the rules of competition, forcing once-dominant players to struggle for survival – much as bookstores and film manufacturers have struggled in the age of e-books and digital cameras.
Convergence could unfold slowly in the vast Machinery sector. Many companies may be disinclined to change. But some, at least, will be stirred by the profound competitive advantages they may gain as first movers. Machinery companies that successfully harness the full potential of digitization, additive manufacturing, cloud computing and other advances will be able to offer customers completely customized solutions that provide highly differentiated value. Convergence will also enable some Machiner y firms to enter (or even create) lucrative new markets. The specifics are impossible to foresee, but over time convergence promises to dramatically expand the Machinery sector’s market footprint … from innovative sourcing to integrated supply chain to engaging customers through a variety of online means, both in manufacturing and services.
Machinery leaders are challenged to bring together diverse elements to create an entirely new entity. Something much more than a traditional Machinery company.
When contemplating convergence, the obstacles loom as large as the possibilities. How, for example, will traditional Machinery firms, steeped in a mechanical culture and mindset, leverage something so radically new as cloud computing? Who will creatively tap the power of big data to bring commercially robust new solutions to customers? Who has the breadth of knowledge to make the company’s solutions the best fit for the larger, ever more complex systems of which they will be a part? Above all, who will interpret all that complexity to make sound strategic choices?
Fundamental Levers
To be a leader in the era of convergence, Machinery executives must optimize three fundamental, highly interdependent levers:
1) Diversity (of expertise) – Engineers tend to specialize very early on, choosing for example either a Mechanical or Software engineering track. As such, individuals who possess a deep understanding of multiple engineering disciplines (as well as cloud based services, sensor technology, 3D printing and the like) are extremely rare. And with every part of the technology landscape in flux, no individual can keep pace with all that is applicable, valuable and relevant. That makes diversity imperative. Not gender or ethnic diversity, but diversity of expertise, experience and perspective. To fully leverage cutting-edge technology, Machinery executives must forge cohesive, high-performing organizations that effectively blend diverse talent from multiple disciplines and backgrounds.
At the leadership level, some Machinery companies are already more diverse than others in terms of expertise, experience and perspective. This could serve them well as they grapple with cross-industry convergence.
Machinery companies can cultivate diversity by adjusting how they rate and develop talent within their own ranks, and by attracting top talent from other sectors. There are several reasons to believe that forward-thinking Machinery companies will be able to attract more technology talent. First, many Machinery companies are already quite high tech and are rapidly becoming more so, which should make them increasingly attractive. Some have already demonstrated they can attract top talent from other industries, especially at senior levels including Board Directors, Chief Executive Officer, Chief Technology Officer, Chief Procurement Officer and Chief Supply Chain Officer. Several Machinery companies have entrusted their futures to executives who – though lacking Machinery sector experience – are proven visionaries, magnets for great technology talent, and inspirational leaders. Clearly, some in the Machinery sector are already moving to compete in a fast-changing world.
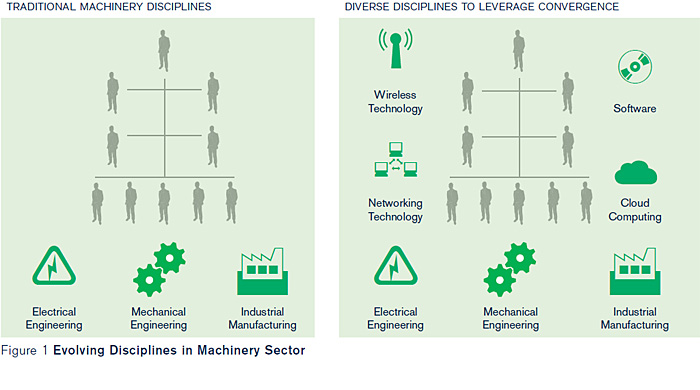
2) Culture – To mold diverse talent together, Machinery companies must evolve toward more open, collaborative cultures that intrinsically value creative freedom, dissimilar perspectives, and far-reaching innovation as much as they have traditionally valued predictability and conformance to specifications. What would such a culture look like? No one can say for sure. It would be both overly simplistic and grossly insufficient to suggest: “Machinery companies must become like High Tech companies.” Simplistic, because Machinery companies cannot simply transform their culture into one that stemmed from a completely different tradition. Insufficient, because the Machinery sector’s future will demand organizational capabilities beyond those currently possessed by any High Tech company.
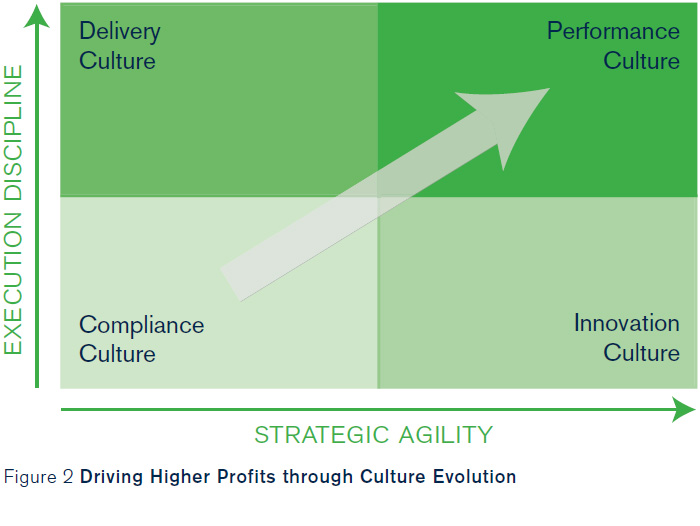
At a minimum, Machinery companies must learn how to work at a much faster pace. That means, in part, evolving from today’s relatively regimented organizations into more freeflowing entities that support concurrence of engineering, project management, manufacturing and service. Machinery company cultures will also need to expand their risk tolerance, more readily accept constructive mistakes, and resist the impulse to reject breakthrough thinking as impractical and unrealistic. The most adaptive Machinery company cultures will balance their traditional emphasis on execution with the new imperatives of fostering speed and creativity, nurturing the many different kinds of talent required to actualize convergence, and creating the cohesion to make it all work together.
This is not to suggest that the transition from a culture primarily focused on operating efficiency to one that is also nimbly adaptive, innovative and smart is simple or easy. Avoiding (or at least surviving) the potential death valley that lay between two such markedly different cultures requires vision, courage, and a sustained focus on results – as the company must continue to perform throughout the transition.
The imperative for Machinery executives now is to weigh their own readiness to lead in the world as it is and may soon be, not as it once was.
Valuable lessons can be drawn from existing Machinery company cultures. While most companies in the sector seem content to make industry average operating profits, a few firms consistently earn margins approaching twice or three times this average. Why? At least part of the difference is their ambition and daring. Overall, the sector has long viewed an average return as acceptable, and so most companies feel little pressure to stretch for more. Yet in certain instances, Machinery CEOs (including a few who came over from industries where profit margins traditionally run higher) have pushed their companies to be more aspirational and have forged company cultures that earn returns much higher than the industry average. In short, the performance disparity that already exists within the sector suggests that the culture change needed for the era of convergence can significantly improve earnings in the present.
As convergence unfolds, a performance culture could transform the earnings paradigm. Certain Machinery companies have applied vision, daring and discipline that have led to adding a percentage point per annum to their operating profit during the past decade, despite some historically adverse economic cycles, while logging comparably solid sales growth in relatively mature, slow-growth market sectors. Convergence could compound growth differentials in both sales and earnings dramatically. Machinery companies with performance cultures (i.e. strategic agility and innovation leadership coupled with strong execution discipline) will then be positioned to grow their market capitalization outpacing their industry peers.
3) Leadership – Leadership might rightfully be called the most fundamental lever, as the changes required for Machinery companies to effectively advance into the Digital Age start at the top.
Traditionally, Machinery companies have been led by executives whose priorities are client interface, technical excellence, differentiated quality, and steady incremental gains in machine and system productivity. As convergence disrupts the sector, Machinery company executives will be compelled to pursue a wider array of objectives and to demonstrate a broader range of leadership strengths. In the midst of technological rev olution, operational excellence will no longer suffice. Rather, Machinery executives must shrewdly and insightfully determine how their own company will get out front in the Digital Age.
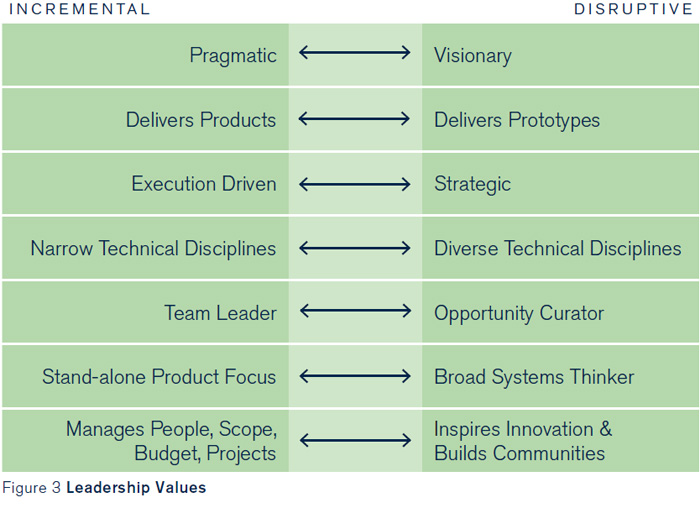
In addition to grappling with the many strategic implications, Machinery executives must learn to be increasingly tolerant of people who think and do things differently. Most will be challenged, sooner or later, to reengineer their organizations to reward more risk taking and innovation, more fully develop internal talent (e.g., by exposing them to more par ts of the disruption, creation and innovation process), and increasingly empower people to pursue disruptive innovation. That means, in part, leading by values versus control – that is, building the “right” behaviors into their company’s DNA, then stepping back to give creative people the freedom they need to be happy and effective in their work.
In short, Machinery executives must grow as leaders. Serious leadership growth begins with awareness that the status quo is less than ideal in the present, and may prove untenable in the future. Both are now true for much of the Machiner y sector. Forward-thinking Machinery leadership teams will view themselves with fresh eyes, and will be both curious and open minded in weighing the practical implications and ramifications of convergence.
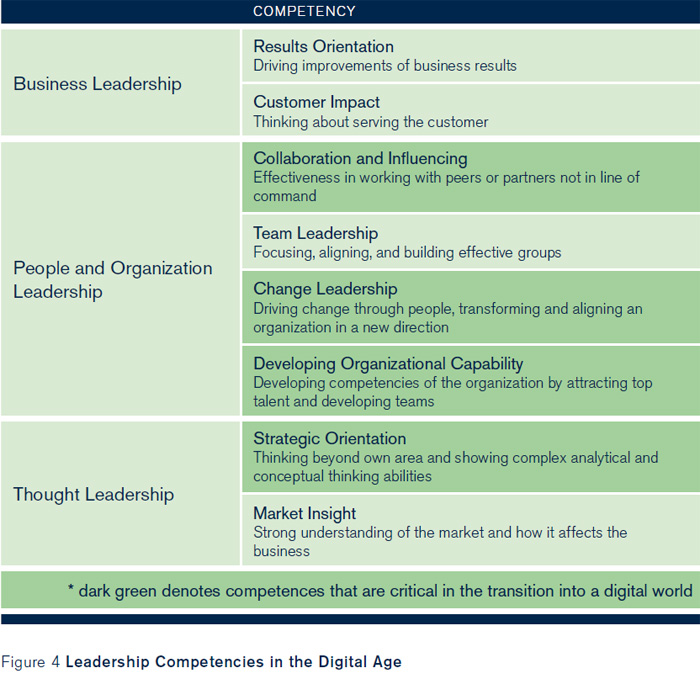
Talent Strategies for the Digital Age
No one can discern with precision what changes the ongoing advances digital technology in manufacturing will bring, but this much is clear – the potential for disruption is too big to ignore. The Digital Age is upon us. It calls for bold thinking by Machinery company executives and boards.
In practical terms, that means charting a fresh course for the company. Key steps in the process include:
Create a sense of urgency. Recognize, study, and clarify the company’s strategic imperative to change. Resolve to adapt before you face a burning platform.
Adopt a systems mindset. The essence of the Digital Age is interconnection (i.e., machinery, servers, data, communication networks). Deepen companywide awareness that your solutions will increasingly be pieces of a much larger puzzle. Craft your future value-add in a macro systems context.
Focus the board on the future. Enhance the board’s understanding of the specific ways digitization may change the competitive landscape. Proactively build board acceptance for new strategies.
Assess and adapt your culture. Gauge the degree to which your current culture is suited to succeed in an “unknowable” future. Increase the value you place on agility and speed, constructive risk taking, and out-of-the-box thinking. As an executive team, clearly communicate the targeted changes in cultural norms, and visibly model essential new behaviors.
Grow your leadership capability. Identify and promote more “horizontal thinkers” who can bring together ideas from multiple disciplines to build the machiner y systems of tomorrow. Invest in attracting leaders who have successfully crafted complex, multidiscipline systems in other contexts.
Experiment. Big successes are born from small failures. Actively experiment with new strategies while carefully containing the risk. Build on what you learn.
Perform. Sustain focus on where the money comes from today as you try out new approaches and foster a more adaptive and innovative performance culture.
Machinery companies that fail to recognize how fluid the environment may become could find themselves at a significant, potentially insurmountable disadvantage, while those who seize the vast opportunities in convergence and move decisively to adapt can effectively position themselves to enjoy employer of choice accolades, sticky customers, and unprecedented shareholder returns.
Pavan Vohra (1962-2016) contributed to this expertise as Co-Author.